Seventh aiCAMstir Meeting, 26 January 2023: Difference between revisions
Jump to navigation
Jump to search
Line 127: | Line 127: | ||
[[File:Reza Beygi and LFM da Silva Effect of FSW Tool Geometry on the Joint Quality of AA2024-T3AA7075-T6 Joints-page-018.JPG|thumb|left|upright=3.2|alt=Reza Beygi and LFM da Silva: Effect of FSW Tool Geometry on the Joint Quality of AA2024-T3AA7075-T6 Joints|Results and discussion: | [[File:Reza Beygi and LFM da Silva Effect of FSW Tool Geometry on the Joint Quality of AA2024-T3AA7075-T6 Joints-page-018.JPG|thumb|left|upright=3.2|alt=Reza Beygi and LFM da Silva: Effect of FSW Tool Geometry on the Joint Quality of AA2024-T3AA7075-T6 Joints|Results and discussion: | ||
Interaction plot]] | Interaction plot]] | ||
[[File:Reza Beygi and LFM da Silva Effect of FSW Tool Geometry on the Joint Quality of AA2024-T3AA7075-T6 Joints-page-019.JPG|thumb|left|upright=3.2|alt=Reza Beygi and LFM da Silva: Effect of FSW Tool Geometry on the Joint Quality of AA2024-T3AA7075-T6 Joints|]] | [[File:Reza Beygi and LFM da Silva Effect of FSW Tool Geometry on the Joint Quality of AA2024-T3AA7075-T6 Joints-page-019.JPG|thumb|left|upright=3.2|alt=Reza Beygi and LFM da Silva: Effect of FSW Tool Geometry on the Joint Quality of AA2024-T3AA7075-T6 Joints|Conclusions: | ||
[[File:Reza Beygi and LFM da Silva Effect of FSW Tool Geometry on the Joint Quality of AA2024-T3AA7075-T6 Joints-page-020.JPG|thumb|left|upright=3.2|alt=Reza Beygi and LFM da Silva: Effect of FSW Tool Geometry on the Joint Quality of AA2024-T3AA7075-T6 Joints|]] | Main results]] | ||
[[File:Reza Beygi and LFM da Silva Effect of FSW Tool Geometry on the Joint Quality of AA2024-T3AA7075-T6 Joints-page-020.JPG|thumb|left|upright=3.2|alt=Reza Beygi and LFM da Silva: Effect of FSW Tool Geometry on the Joint Quality of AA2024-T3AA7075-T6 Joints| Conclusions: | |||
Main results: | |||
- ANN was successfully used to understand the effect of welding parameters and tool geometry on the ultimate | |||
tensile strengths of the welds. The optimum condition was obtained by the SA method which corresponded to the | |||
experimental result successfully. <br/> | |||
- All the joints possessed a root defect at a low rotation speed of the joint due to a lack of material flow under the | |||
pin. <br/> | |||
- The joints made by the pyramidal pin possessed the lowest joint strengths due to the various welding defects at | |||
different tool rotation speeds: At 1200 rpm the lack of plastic flow, at 1000 rpm the banding structure, and 800 rpm | |||
the root defect. <br/> | |||
- The joints made by the conical pin were free of defects at higher rotation speeds but still had a low tensile | |||
strength. This was attributed to the softening caused by the precipitates coarsening in the stir zone due to a high | |||
temperature during welding. <br/> | |||
- The UTS of the welded specimens had little sensitivity to the welding speed. <br/> | |||
- The optimum joint strength was obtained using the cylindrical tool at high rotation speed where the root defect | |||
disappeared due to enough material flow. This tool having a low volume did not cause a high temperature during | |||
welding and therefore softening was minimized.]] | |||
[[File:Reza Beygi and LFM da Silva Effect of FSW Tool Geometry on the Joint Quality of AA2024-T3AA7075-T6 Joints-page-021.JPG|thumb|left|upright=3.2|alt=Reza Beygi and LFM da Silva: Effect of FSW Tool Geometry on the Joint Quality of AA2024-T3AA7075-T6 Joints|]] | [[File:Reza Beygi and LFM da Silva Effect of FSW Tool Geometry on the Joint Quality of AA2024-T3AA7075-T6 Joints-page-021.JPG|thumb|left|upright=3.2|alt=Reza Beygi and LFM da Silva: Effect of FSW Tool Geometry on the Joint Quality of AA2024-T3AA7075-T6 Joints|]] | ||
<div style="clear:both;"> | <div style="clear:both;"> |
Revision as of 12:24, 27 January 2023
The Seventh aiCAMstir Meeting was held online on 26 January 2023 with 32 attendees.
Agenda
The agenda of the 90 min long on-line meeting was as follows:
- Welcome and introduction (2-3 sentences each)
- Development of a new stitch friction stir welding gun and mechanical behavior of intersecting stitch welded AA 6016-T4 sheets. Dominik Walz, MPA Stuttgart, Germany (20 min + 5 min questions)
- Effect of FSW tool geometry on the joint quality of AA2024-T3/AA7075T6 joints in butt configuration. Reza Beygi, INEGI, Porto, Portugal (20 min + 5 min questions)
- Machine investment cost and tool wear of friction stir welding of battery trays of compact crossovers. Stephan Kallee, AluStir, Germany (20 min + 5 min questions)
- Collaborative projects, organisational comments and date of next meeting (25 May 2023). Mike Lewis (FTS Engineering Answers Ltd)
Presentations
Development of a new stitch friction stir welding gun and mechanical behavior of intersecting stitch welded AA 6016-T4 sheets. Dominik Walz, MPA Stuttgart, Germany
Effect of FSW tool geometry on the joint quality of AA2024-T3/AA7075T6 joints in butt configuration. Reza Beygi, INEGI, Porto, Portugal
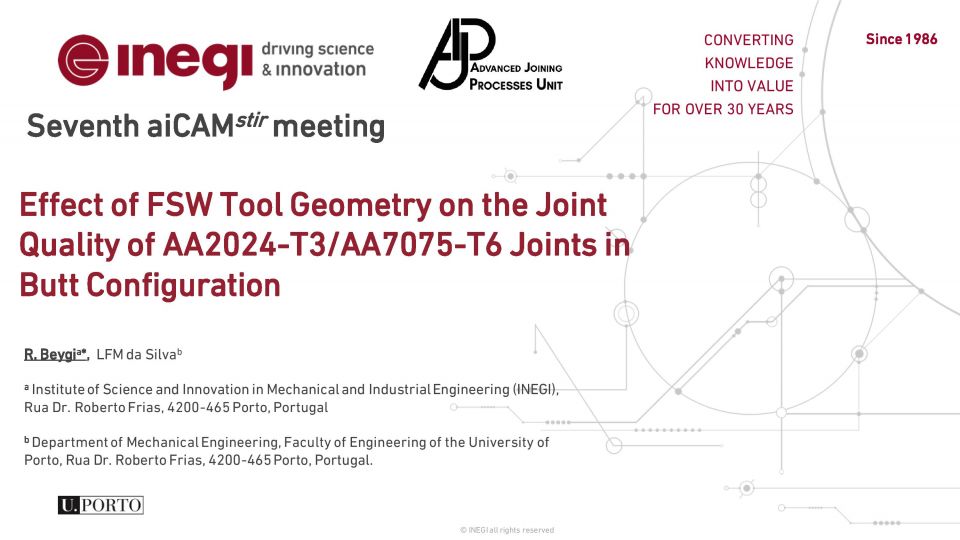
R. Beygia (Institute of Science and Innovation in Mechanical and Industrial Engineering (INEGI), Rua Dr. Roberto Frias, 4200-465 Porto, Portugal) and LFM da Silva (Department of Mechanical Engineering, Faculty of Engineering of the University of Porto, Rua Dr. Roberto Frias, 4200-465 Porto, Portugal): Effect of FSW Tool Geometry on the Joint Quality of AA2024-T3/AA7075-T6 Joints in Butt Configuration. Seventh aiCAMstir meeting, 26 January 2023
Conclusions: Main results: - ANN was successfully used to understand the effect of welding parameters and tool geometry on the ultimate tensile strengths of the welds. The optimum condition was obtained by the SA method which corresponded to the experimental result successfully.
- All the joints possessed a root defect at a low rotation speed of the joint due to a lack of material flow under the pin.
- The joints made by the pyramidal pin possessed the lowest joint strengths due to the various welding defects at different tool rotation speeds: At 1200 rpm the lack of plastic flow, at 1000 rpm the banding structure, and 800 rpm the root defect.
- The joints made by the conical pin were free of defects at higher rotation speeds but still had a low tensile strength. This was attributed to the softening caused by the precipitates coarsening in the stir zone due to a high temperature during welding.
- The UTS of the welded specimens had little sensitivity to the welding speed.
- The optimum joint strength was obtained using the cylindrical tool at high rotation speed where the root defect disappeared due to enough material flow. This tool having a low volume did not cause a high temperature during welding and therefore softening was minimized.
- All the joints possessed a root defect at a low rotation speed of the joint due to a lack of material flow under the pin.
- The joints made by the pyramidal pin possessed the lowest joint strengths due to the various welding defects at different tool rotation speeds: At 1200 rpm the lack of plastic flow, at 1000 rpm the banding structure, and 800 rpm the root defect.
- The joints made by the conical pin were free of defects at higher rotation speeds but still had a low tensile strength. This was attributed to the softening caused by the precipitates coarsening in the stir zone due to a high temperature during welding.
- The UTS of the welded specimens had little sensitivity to the welding speed.
- The optimum joint strength was obtained using the cylindrical tool at high rotation speed where the root defect disappeared due to enough material flow. This tool having a low volume did not cause a high temperature during welding and therefore softening was minimized.
Machine investment cost and tool wear of friction stir welding of battery trays of compact crossovers. Stephan Kallee, AluStir, Germany
AluStir Battery Tray, 1.3 x 1.7 m floor plate, Made from hollow aluminium extrusions, 14 parallel friction stir welds: 22 m weld length Cut off the start and stop or park the end hole in a suitable place, Benchmarking study is based on producing trays for 200,000 cars per year in Europe, 100 sec per car
Quality and Cost: aiCAMstir Software, The vision is to develop a software-package that adjusts the parameters automatically based on CFD, analytical modelling, parameter monitoring, image analysis and non-destructive testing, aiCAMstir Ontology, To predict the quality and cost of FSW based on parameters, variables and boundary values
FSW: Ideal for Aluminium, Low distortion, Very reliable process, Use high quality extrusions with good tolerances, Use rigid machines with sophisticated force and position control, Good clamping required, To be welded from one side using a mechanical interlock or from both sides simultaneously, Run-on and run-off tabs are possible
FSW Tools: Wear Mechanisms, Adhesion (tribological reactions): pits and notches (scoring), Diffusion (embrittlement and fatigue): shearing off the pin. Recommendations, Avoid notch between pin and shoulder, Use Triflat instead of Triflute, Reduce the rotation speed, Increase pin diameter, Keep shoulder diameter as small as possible, Use harder materials, Use coatings
Ford Mach-E: Munro: MIG welding, Variation LHS-RHS: robotic and manual or differently programmed, End-crater parked away from the highly stressed zone, Burn-in at the weld start, Consistency and accuracy are required, MIG welding of aluminium is more difficult than MAG welding steel, because you cant see the temperature, Production ramp-up is complicated and expensive
Benchmarking: Munro and Sabic, Expensive tooling for die casting of aluminium, Most OEMs have excellent foundries and want to keep their staff employed, Tray and Total Assembly made from Plastics, Battery Tray: 72 kg vs. 43 kg: Δ 29 kg (weight saving by using plastic), Total Assembly 489 kg vs. 427 kg: Δ 62 kg (cost saving by using plastic)
A video recording of this online meeting is available via the following link:
Recording of the Seventh aiCAMstir Meeting (Total: 1:45 h, the first presentation starts at 0:10:16 h) |
Literature
- äää
Next meeting
We want to invite you to attend the Eight online aiCAMstir Meeting on using artificial intelligence in Computer Aided Manufacture of friction stir welds. The meeting will be held on Thursday, 25 May 2023, 16:00 - 17:30 (London), as shown on upcoming events.
Please contact stephan.kallee@alustir.com, if you want to attend the meeting and/or if you want to participate in the project.